Mastering the Low Pressure Casting Process
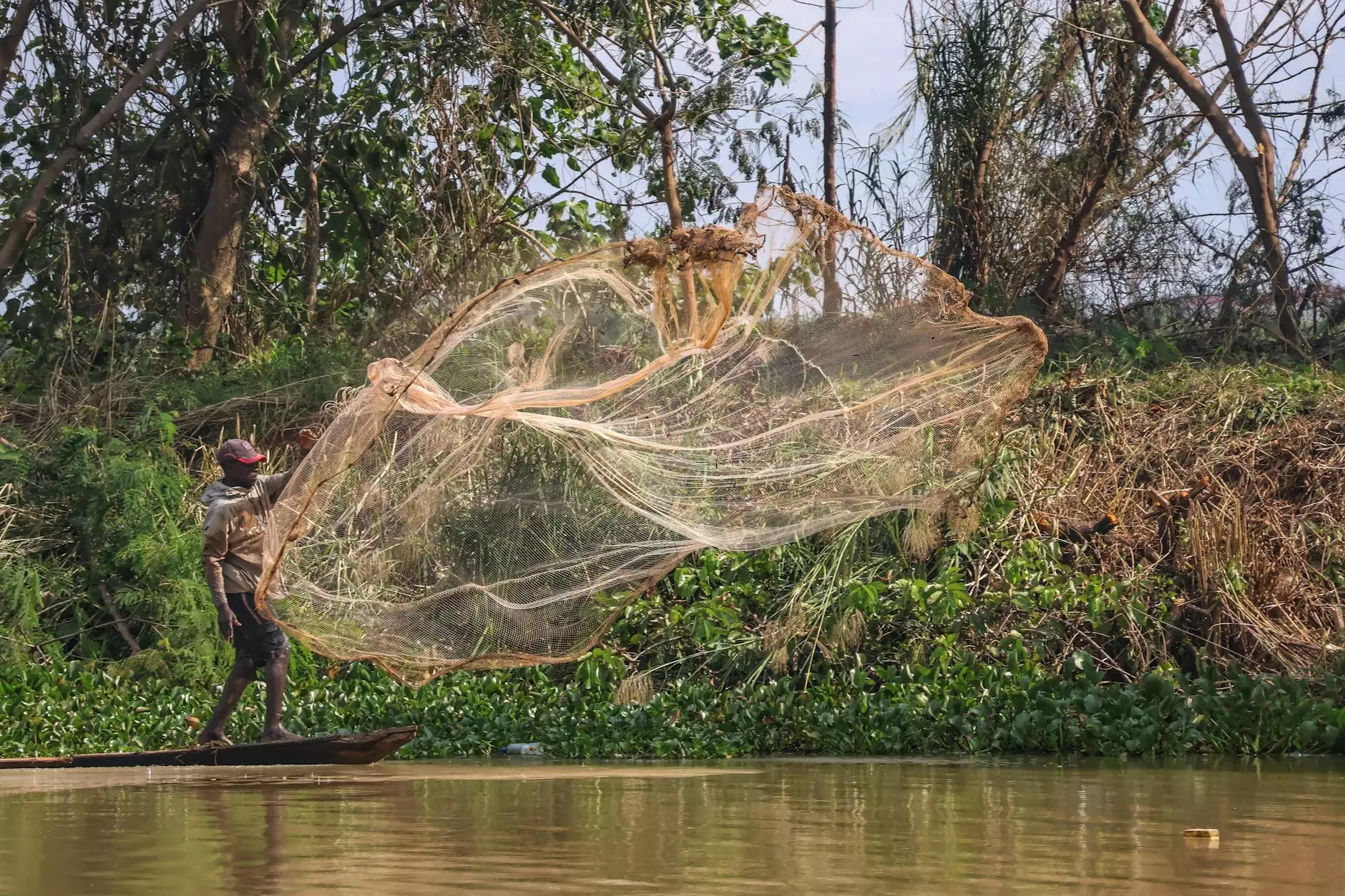
The low pressure casting process is an innovative manufacturing method that has garnered significant attention in various industries, notably in product design and 3D printing. This article delves deeply into the nuances of this process, shedding light on its advantages, applications, and benefits, particularly for businesses like arti90.com that specialize in art supplies.
What is Low Pressure Casting?
The low pressure casting process is a technique where molten metal is injected into a mold under low pressure. This approach contrasts with traditional casting methods and presents several distinct advantages, especially when it comes to producing high-quality parts.
Key Features of Low Pressure Casting
- Controlled Pressure: Utilizing low pressure allows for better control over the flow of molten metal, reducing the risk of defects.
- High Precision: This process can produce intricate designs with exceptional accuracy, making it suitable for detailed product features.
- Material Efficiency: Minimizes waste as the controlled flow ensures that the right amount of material is utilized.
- Rapid Production: Enables faster cycle times, which is essential for businesses aiming for shorter lead times.
Advantages of the Low Pressure Casting Process
Understanding the benefits of the low pressure casting process can help businesses streamline their production and improve their product offerings. Here are some notable advantages:
1. Reduces Defects
One of the primary benefits of the low pressure casting process is the significant reduction in the number of defects. Traditional casting methods often lead to issues such as air bubbles and uneven distribution of materials. The low pressure environment minimizes these risks, resulting in a higher quality final product.
2. Improved Surface Finish
The low pressure casting process provides a smoother surface finish compared to other casting techniques. This is essential for art supplies where aesthetic quality is paramount. Artists and designers benefit from a product that requires less post-processing, saving time and costs.
3. Greater Versatility in Materials
This casting method is not limited to specific types of metals, allowing for greater versatility in material selection. Whether it’s aluminum, magnesium, or zinc alloys, the low pressure casting process can accommodate a range of materials, thus meeting the varied demands of different industries.
4. Environmentally Friendly
With a reduced amount of waste and the capability to recycle materials, the low pressure casting process aligns well with today’s sustainability goals. Businesses that prioritize eco-friendly practices can appeal to a larger customer base that values environmental responsibility.
Applications of the Low Pressure Casting Process
The versatility of the low pressure casting process makes it applicable across various sectors, from product design to automotive manufacturing. Below are some notable applications:
1. Artistic Components and Art Supplies
In the realm of art supplies, the low pressure casting process is used to create stunning components for sculptures, designs, and custom tools. Artists benefit from the precision and quality that this method provides.
2. Automotive Parts
Automotive industries frequently utilize this casting method for manufacturing components like engine blocks and transmission cases. The durability and lightweight nature of the parts produced through this process contribute to overall vehicle efficiency.
3. Aerospace Components
The aerospace industry demands the highest quality for its parts. Low pressure casting is ideal for creating components that can withstand extreme conditions while maintaining structural integrity.
4. Custom Prototyping
Rapid prototyping is another significant application area. With the ability to produce high-precision molds quickly, businesses can test designs and iterate more efficiently, which is especially beneficial for product developers and innovators.
How the Low Pressure Casting Process Works
To fully appreciate the low pressure casting process, it’s essential to understand the steps involved:
Step 1: Mold Preparation
The first step involves designing and preparing the mold. The mold is created from durable materials and is engineered to withstand the low pressure environment.
Step 2: Heating the Metal
The metal intended for casting is heated until it reaches a molten state. Precise temperature control is essential to ensure the quality of the cast.
Step 3: Injection of Molten Metal
Under low pressure, the molten metal is injected into the mold. This step is crucial as the pressure ensures that the metal fills all cavities of the mold without any gaps.
Step 4: Cooling and Solidification
Once the mold is filled, it is allowed to cool. The cooling process solidifies the metal into the desired shape. This can take anywhere from a few minutes to several hours, depending on the thickness of the cast.
Step 5: Mold Removal and Finishing
After the metal has cooled and solidified, the mold is opened, and the cast part is removed. Additional finishing processes may be applied to achieve the desired surface quality.
Future of Low Pressure Casting in 3D Printing
As the landscape of manufacturing evolves, the integration of low pressure casting with 3D printing technology presents exciting possibilities. This combination promises to revolutionize the way products are designed and produced.
Adoption of Advanced Materials
With advancements in material science, the potential for using new alloys and composites within the low pressure casting process expands. These materials can offer enhanced properties such as increased strength or better heat resistance.
Custom Design Integration
The synergy between 3D printing and low pressure casting allows for the creation of highly customized designs that can seamlessly transition from digital to physical form. This is particularly advantageous for designers looking to push the boundaries of creativity.
Cost and Time Efficiency
Combining these two technologies can lead to significant reductions in production time and costs. As businesses strive for efficiency, adopting such innovative processes is essential to remain competitive in the market.
Conclusion
In summary, the low pressure casting process represents a leap forward in manufacturing capabilities, offering distinct advantages from improved quality to increased efficiency. As businesses like arti90.com harness this technology, they position themselves at the forefront of innovation in the art supplies sector, driving progress in product design and 3D printing. By understanding and utilizing this process, businesses can not only enhance their product offerings but also cater to the ever-evolving demands of their customers.